Cable Actuated Disc Brake Braking Performance
- edwu91
- Feb 7, 2022
- 5 min read
This is my analysis and testing of cable actuated hydraulic brakes (CAHBs) for bikes. There will be equations and technical descriptions. At the end, there will be a TL;DR for those that want to skip the summary of ways to improve braking performance.
Table of Contents:
The Problem:
CAHBs have always been considered inferior to fully hydraulic systems. It takes a lot of grip strength to stop with CAHBs, the braking can’t be modulated, and can feel “spongy”. Below I’ll attempt to convey what I think are important attributes impacting braking. We’ll look at cable housing compression, cable friction, and mechanical advantage.
Overview:
Brakes turn kinetic energy you generate moving forward into heat. Brake pads squeeze the brake rotor to slow you down. Heat is generated as you slow down. The heat generated is equal to the kinetic energy you lose. Other factors such as aerodynamic drag, rolling friction, tire traction* will be ignored.
I’ll specifically be looking at the CAHBs I purchased to fit on my Chinese bike.
I’ll look at how compressionless cables impact the braking performance.
*tires also make a considerable difference to braking and shouldn’t be ignored outright. Further analysis will be done breaking down how tires impact braking. For now, this is somewhat an incomplete analysis.
Braking Analysis:
As you squeeze the brakes, you apply a force F_N on the rotors via the brake pads. That force on the rotors is friction as is related to the force applied by the equation below:

Diagram below shows how your input force (F_N), friction force (F_Fr), and the tangential portion of the rotor’s inertial force are related in a vector diagram.
We’ll look into F_N in more detail as this makes up the majority of where the brake “feeling” comes from

User Braking Force:
There is a relationship between user input force and a bunch of parameters. Below is a simple set of equations that get us to a useful form.
Note: this equation only looks at one brake lever.

Analysis:
Two interesting features arise from this.
1) your speed has by for the greatest impact on how much force/energy is required to stop. The faster you go, the bigger your brakes should be.
2) Rotor and wheel size plat a role in your stopping distance. The bigger your rotors are, the easier it is to brake. The smaller your effective wheel diameter is, the easier it is to brake. You can think of relationship between wheel and rotor as the braking mechanical advantage ratio .
The plot below shows the relationship between cable tension and rotor diameter for a user stopping from 30 - 0Kph on wheels with diameter of 71cm. Assuming a mu_fr ~0.3 and need 5m to stop

You can see that increasing rotor size is an easy way to improve how much force you need to stop. (mass eq. Force = F/g) Note: One can’t arbitrarily increase rotor size on any frame and needs to ensure the frame can accept larger rotors.
System Gain (mechanical advantage):
The equation above only looks at the input force, which is the force from the pistons;
We now translate the piston force to grip force through a series of levers shown below. This provides mechanical advantage. There’s also gain from the hydraulic system in this case. At this point I haven’t measured because I don’t want to disassemble the hydraulic brake yet.
The difference between hydraulic and spring brake calipers is the hydraulic advantage. So in theory, you should get better braking with CAHBs.
Diagram below shows the pivot points and where the forces are located.
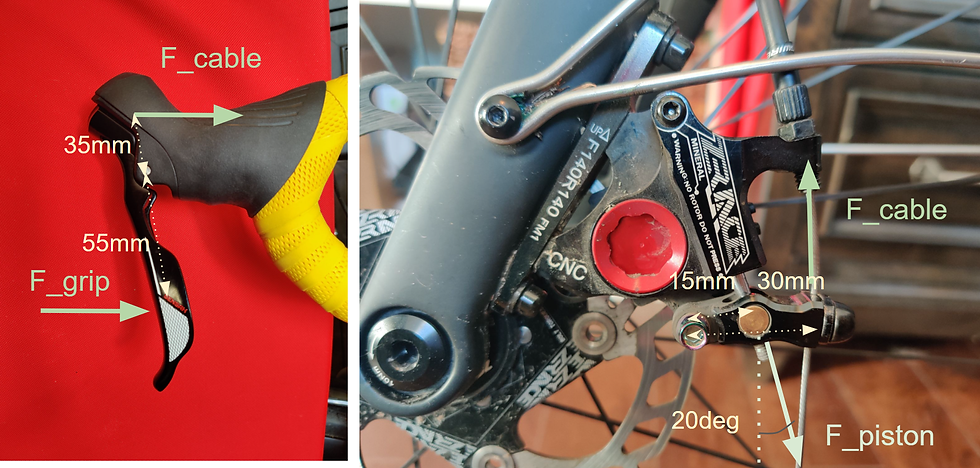
We can then solve a system of linear equations to get a relation between grip force to piston force

This shows a force multiplier of 3.11x to F_piston
In this case, we’ll just assume a hydraulic advantage of F_N ~ 2F_piston
This gives use a total force multiplier of ~6.2
What this shows is that the brake calipers multiply your force considerably. We’ll see below, even with this mechanical advantage, the brakes still take a lot of effort to press. This is likely due to the return spring constant in the piston.
Modulation:
The mechanical advantage is highly dependent on where you pull the lever. If you’re on the tops, you’ll tend to pull closer to the pivot point, reducing your mechanical advantage. The only way to change that is to change the shape of the shifter. I’ve noticed Shimano does a very good job with shift lever ergonomics. Braking on the drops increase your mechanical advantage and slightly improves modulation.
System Losses:
There are two main losses in CAHBs: friction loss and brake housing compression. I conducted a simple test (more qualitative) to compare the two losses.
I’ll be comparing regular cable housing (Shimano 9000) with compressionless cable housing (Jagwire KEB-SL). You can find more information on these types of cable housings here:
The equation governing system loss is below. Note that F_loss is measured at F_grip unless stated in the table below.
F_loss = F_compression + F_friction (static)
The purpose of the test below is to characterize the force loss as best I can.
Test Setup:

I pull the brake lever with a hanging weigh scale to measure the force in kg. I wait until the force stabilizes and take note of how much force is required to pull the brakes just before they touch the rotor. This measures the static friction which should be higher than the kinetic friction.
I took measurements at various locations on the bike with different housing and even against full hydraulic systems. I performed 5 measurements per configuration below and averaged the measurements. The results are tabled below.
Type | Cable housing material | F_loss (kg) |
Front CAHB (F_1) | Shimano housing (900mm) | 2.11 |
Front CAHB (F_2) | Jagwire housing (900mm) | 1.72 |
Rear CAHB (F_3) | Shimano housing (1800mm) | 2.66 |
Rear CAHB (F_4) | Jagwire housing (1800mm) | 1.61 |
CAHB (F_5) | Jagwire housing (900mm) | 1.3 |
CAHB (F_6) | Measured at F_cable on brake caliper | 2.09 |
Shimano 105 hydraulic brakes | N/A | 0.5 |
Shimano RS785 brakes | N/A | 0.51 |
Test Result Review:
F_Friction doesn’t vary that much with respect to cable length and number of bends.
We can see from diagram above that F_6 is roughly equal to F_5 when scaled by the mechanical advantage of the lever.

The error can be explained by my lazy test procedure. The tests show little/no compression or friction losses in F_5. While this doesn’t mean there is no compression losses ever in compressionless housing, I’ll just make that assumption for now.
What test F_6 also shows is that a lot of force is required to overcome the return spring. Changing the spring constant to something slightly less might make dramatic improvements to braking.
The table shows that when routed on the bike, we see F_Friction = 400g ~ 32% increase in pull force required (F_2). The major losses are likely where the cable makes the sharpest bends. Longer housing didn’t increase the force required, which likely means the friction is heavily dependent on number of bends and bend radius.
Lots of force is needed to overcome the losses in the regular brake housing system. 1Kg for the rear brake and 500g in the front.
Sponginess:
Sponginess in this case is wasted energy used to elastically deform an object. Therefore, brake sponginess is 100% related to F_compression. As you eliminate F_compression, the sponginess disappears. From the table above, you can see braking force improvement of 20% (Front) 37% (Rear).
Ride Review of CAHB:
Switching to compressionless really helps with braking and is probably all you’ll really need. Where it starts to become problematic is when you are riding terrain that requires lots of braking force. Bike handling skill helps make CAHBs manageable on technical terrain; however, if you descend technical terrain on the tops, I would recommend against them unless you are interested in a hand workout as with your bike ride.

TL;DR;
CAHB see a significant performance boost with compressionless housing.
Gets rid of brake sponginess
Slightly improves modulation
Larger rotor sizes decrease the amount of force required to brake
A decent amount of the losses are attributed to the return spring in the piston. Future improves can be easy part replacement
Hand position/shifter ergonomics can play a role in braking
Braking on the drops can offer slight modulation
Commentaires